A manufacturing business operates with complexities in the world of making things, from toys to tools. The manufacturing process needs careful accounting to keep everything running smoothly.
Accounting for manufacturing includes keeping an eye on the cost of everything used in the production process, from the electricity that powers machines to the materials shaped into products, following generally accepted accounting principles. It's like a detailed grocery list (bill of materials) and a careful budget (job costing), ensuring the total cost doesn't eat into profits.
With the help of manufacturing software, it's easier to manage inventory, figure out the average cost of making each item according to accounting standards, and ensure there's enough on the shelf without overflowing. This careful balancing act ensures the manufacturing business can whip up its products efficiently and cost-effectively, just like a master chef.
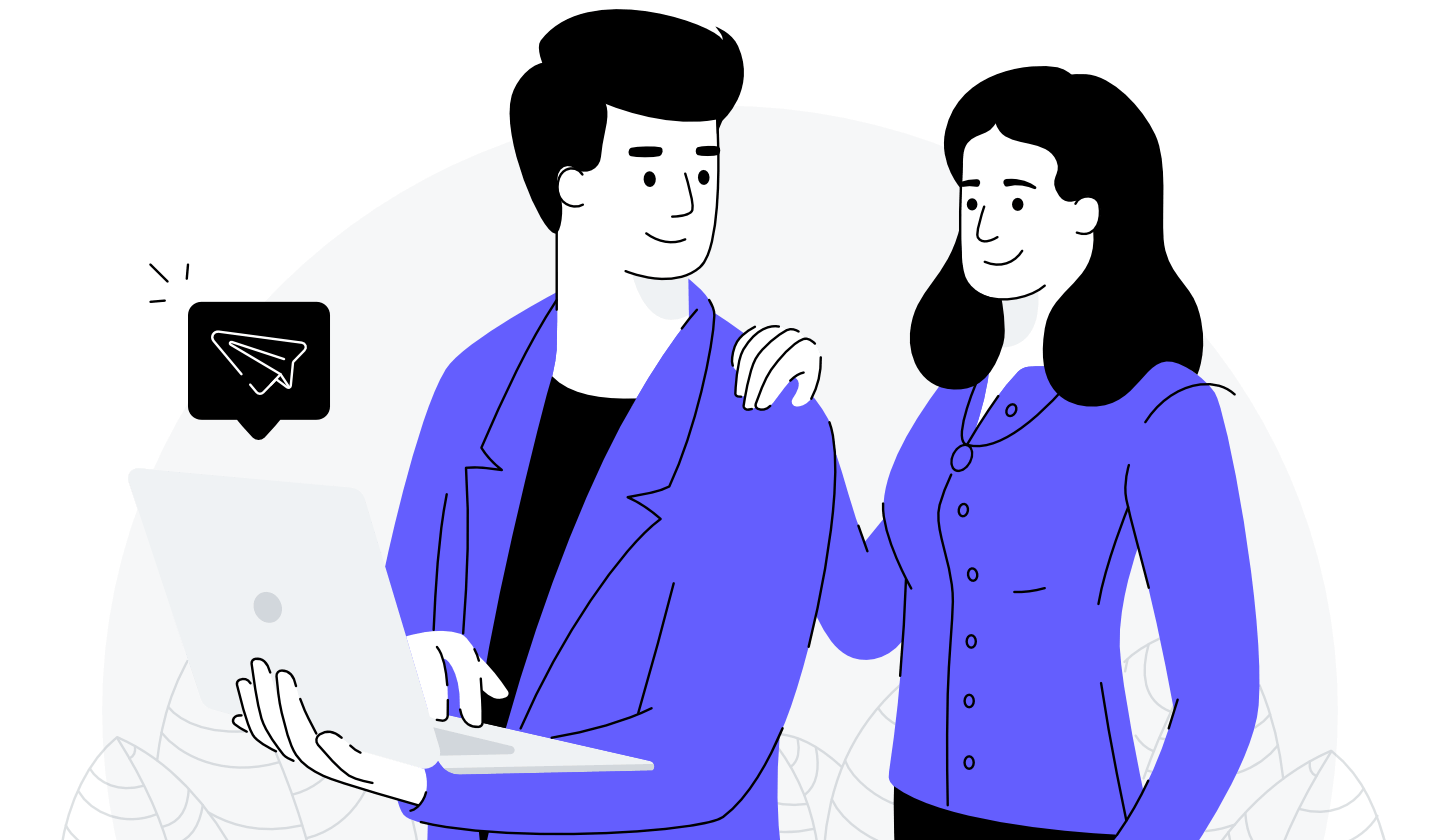
What is Manufacturing Accounting, and Why is it Important?
Manufacturing accounting is like the navigational system of a ship, guiding manufacturing operations through the vast sea of financial management to ensure a smooth journey toward profitability, a cornerstone in understanding everything you need to know about manufacturing accounting.
Understanding the Basics of Manufacturing Accounting
Manufacturing accounting is the backbone of understanding the costs associated with producing goods. It tracks direct material, direct labor, and manufacturing overhead, painting a clear picture of the product cost. This process is crucial for keeping inventory levels in check and ensuring the accounting process aligns with the physical flow of goods.
Importance of Accurate Manufacturing Accounting for Businesses
Accurate manufacturing accounting ensures businesses can confidently sail through financial uncertainties, thanks to comprehensive accounting data. It provides a detailed insight into the indirect costs and total cost of manufacturing, helping companies to evaluate their profitability. This accuracy in determining the cost of producing a product is vital for strategic decision-making and maintaining healthy inventory management practices, aligning with generally accepted accounting principles.
Benefits of Implementing Manufacturing Accounting Systems
Implementing manufacturing accounting systems, especially those designed for discrete manufacturing, is like automating the ship's course, allowing for a more efficient journey. These systems help automate the manufacturing accounting process, from tracking production costing methods to monitoring inventory levels, thus aiding manufacturing accountants in their daily tasks. The result is a streamlined operation that enhances the accuracy of financial reporting and supports the overall growth of manufacturing operations through the use of manufacturing ERP.
Key Elements of Manufacturing Costing
Understanding manufacturing costing is like assembling a complex machine; every part must fit perfectly to work efficiently.
Overview of Manufacturing Costs and Costing Methods
Manufacturing businesses can file taxes with an understanding of manufacturing accounting tracks to determine the cost of producing a product, ensuring all costs associated with manufacturing are accurately reported. This includes direct material costs, direct labor costs, manufacturing overhead, and other direct and indirect costs used in manufacturing. Costing methods, like process or batch costing, determine how much it costs to produce a batch of products or a single item, ensuring accurate costing and financial reporting.
Exploring Overhead Costs in Manufacturing
Overhead costs, encompassing direct and indirect costs, are like the oil that keeps the machine running but isn't part of the main engine. These indirect costs, such as electricity, maintenance, and rent, might not be directly tied to producing a product but are essential for manufacturing operations. Knowing these costs is crucial for pricing products correctly and for profitability.
Inventory Valuation Techniques in Cost Accounting
Inventory valuation is about keeping track of the cost of materials, work in process, and finished goods, an essential process in both discrete and process manufacturing. Techniques like First In, First Out (FIFO) or Last In, First Out (LIFO) help assess the value of inventory on hand and the cost of goods sold. An accurate inventory system prevents excess inventory and helps make informed decisions about production needs.
Choosing the Right Manufacturing Accounting Software
Selecting the right tools for managing manufacturing accounting, such as manufacturing ERP systems, is crucial for ensuring the gears of your business run smoothly.
Factors to Consider When Selecting Accounting Software for Manufacturers
When picking accounting software, manufacturers need to consider factors such as its ability to handle the accepted accounting principles, its integration with inventory costing, and its capacity for financial statements and reporting. The chosen accounting method should offer detailed insights into material costs, direct and indirect labor costs, and overhead, enabling accurate financial reporting and decision-making.
Integration of ERP Systems in Manufacturing Accounting
ERP (Enterprise Resource Planning) systems, specialized software for manufacturing, are like the central processing unit of a manufacturing company's operations, integrating various functions from inventory management to accounting. An ERP system that integrates seamlessly with your manufacturing accounting process can automate many tasks, providing a comprehensive overview of your financials, inventory levels, and the total cost of producing products. This is vital for producing accurate financial statements and making informed decisions.
Further Reading: Learn How Partnerships Are Taxed
Optimizing Production Cost Management
In the world of making things, keeping an eye on how much everything costs is key. Just like a chef needs to know the price of ingredients, including the cost of raw materials, to make a delicious and profitable meal, manufacturing companies need to be smart about their spending.
Best Practices for Controlling Production Costs
Manufacturing accountants are like the guardians of the treasure chest, ensuring no coin is wasted, epitomizing the precision and efficiency of modern manufacturing accounting. They follow certain best practices, such as cost accounting methods focusing on manufacturing costs. This includes tracking direct costs like materials and labor and tricky indirect costs like electricity or rent, showcasing how manufacturing accounting includes accounting data on all operational expenses. It's all about making sure the total manufacturing cost stays as low as possible without cutting corners, in accordance with best accounting practices.
Improving Cash Flow through Efficient Cost Management
Efficient cost management in manufacturing is like having a well-oiled machine; it keeps everything running smoothly and ensures enough money in the bank to keep the lights on and machines running. By following generally accepted accounting principles (GAAP) and using the right software for manufacturing, businesses can keep a close eye on their cash flow. This form of accounting ensures that every penny spent on producing a product is tracked, from the big stuff like direct labor costs to the smaller, often overlooked manufacturing overhead costs.
Key Takeaways:
- Cost of Production: The total money spent to make products, including materials, labor, and overhead, emphasizes the importance of accounting for manufacturing costs comprehensively, highlighting the critical role of costs associated with manufacturing.
- Inventory: The raw materials, work-in-progress, and finished goods represent different stages of direct and indirect costs, including the cost of raw materials, in the production process. The raw materials, work-in-progress, and finished goods that a manufacturer has, represent different stages of direct and indirect costs in the production process.
- Overhead: A significant aspect of manufacturing accounting, covering all indirect costs associated with manufacturing. In manufacturing industries, overhead includes not just the direct cost of materials and labor but also indirect costs like utilities and rent. The costs to run a factory aren't directly tied to making a specific product, like electricity or rent.
- Gross Margin: A key indicator in manufacturing accounting that focuses on the difference between sales revenue and the costs of goods sold. This important financial metric helps businesses in manufacturing industries understand their profitability by subtracting the cost of goods sold, including direct and indirect costs, from revenue. The difference between sales revenue and the cost of goods sold.
- Break-even Point: The moment when sales revenue equals the total production costs, meaning the business starts to make a profit, is a critical point underscored by manufacturing accounting tracks.
How can Taxfyle help?
Finding an accountant to manage your bookkeeping and file taxes with an understanding of manufacturing accounting tracks to ensure all costs associated with manufacturing are accurately reported. is a big decision. Luckily, you don't have to handle the search on your own.
At Taxfyle, we connect small businesses with licensed, experienced CPAs or EAs in the US. We handle the hard part of finding the right tax professional by matching you with a Pro who has the right experience to meet your unique needs and will manage your bookkeeping and file taxes for you.
Get started with Taxfyle today, and see how finances can be simplified.